The ultrasonic testing
The ultrasonic testing is basic method of non-destructiv testing material. This testing is using ultrasonic waves in the object or material tested. Sound is introduced into the part by using an ultrasonic transducer that converts electrical impulses from the UT machine into sound waves, then converts returns sound back into electric impulses.
With this type of testing is possible to search real defects (duplex, snow flakes), linear defects (cracks, cold joints), cubic defects (pores, draws). If is used suitable combination of machine, the probe is possible to measure wall thickness and coat thickness.
Straight Beam
The control of inside quality of plate thickness 50 mm for defect as doubling, in range of volume.
On the plate surface you can see marks of a gel (called „couplant“), which is used between thae face of the transducer and the surface of the part to allow the sound to be transmitted into the part. Ultrasound not travel through air.
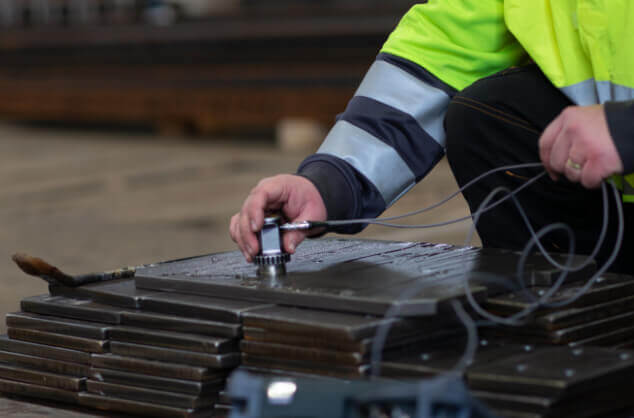
Principal of straight beam
The straight beam inspection uses longitudinal waves transmitted through material. If the material is homogeneous without any inside defects, waves transmitt through material and come back from back-wall to transducer. Distance between two echos depends on material thickness. In the other case the inside defect is in material. The most of sounds come back to tranducer from this defect and of the display you can see third echo, which depends on depth of defect in material.
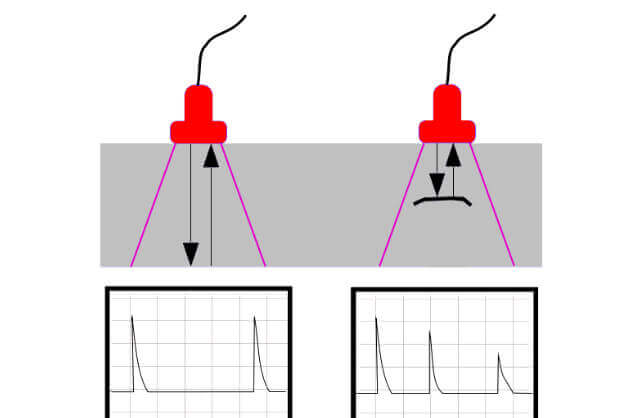
Principal of angle beam
The ultrasound is emited by silicon transducer and it is mounted on an angle wedge. The tranducer and wedge combination is moved back and forth towards the weld so that the probe beam passes through the full volume of the weld. Thanks to good combination of different angles this UT method is very reliable.
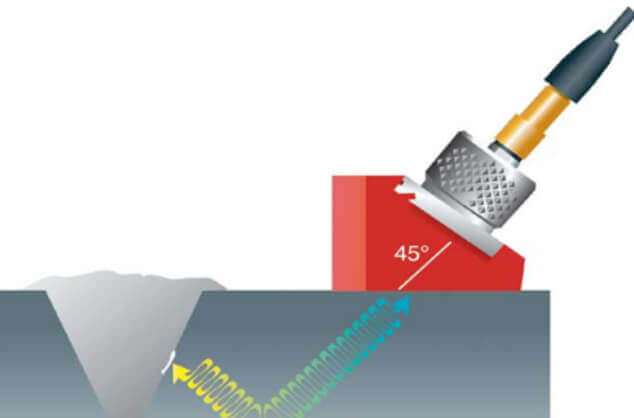
Example of usage
The typical use of this method is – the control of full welded weld joint by angle transducer. By transducer moving on the surface we can check whole volume of weld. On the display you can see echo, which is caused by comeback of sound beam from defect inside the weld. When properly select right combination of all parameters, on the display we can deduct exact position of found defect (depth and position of defect).
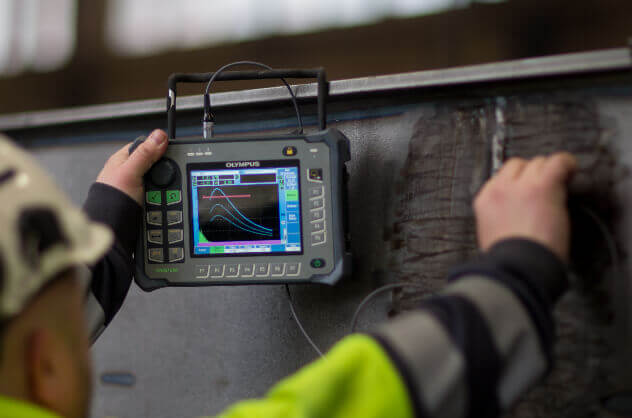
The control is done in three steps acc. to customer’s requirement:
- Inspection of base material before start of welding
- Weld inspection
- Inspection of castings and forgings in all production steps
After all inspections is issued the report acc. to customer requirement. This report contains all necessary information about method, inspection process and inspection results. Acc. to customer requirement is possible to prepare sketch with position of defects in the product. All our UT operators are certified in level 2 acc. to ČSN EN ISO 9712.
Company WELDINSPECT s.r.o.
The company WELDINSPECT s.r.o. is using for UT control tools, which fulfill acc. to rules EN ISO. Then we use necessary calibrating gauges, which are needfull for right calibration of machines.
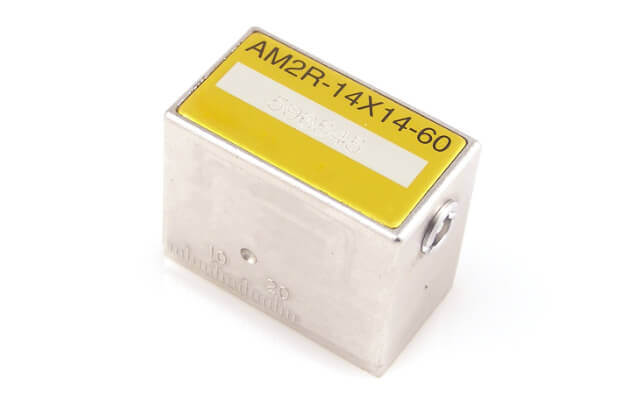
Probe mark SONOSTAR, GE, PNAMETRICS
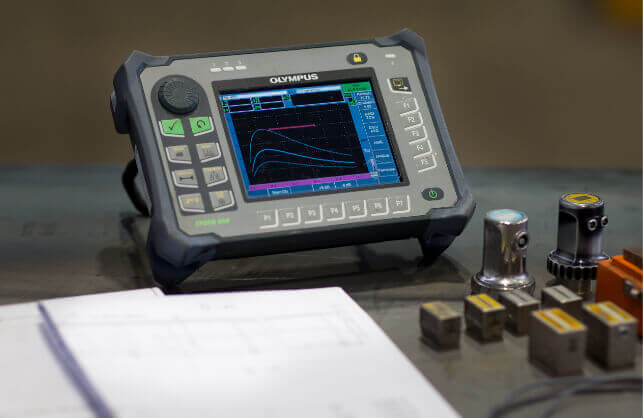
Ultrasonic defectoscop Olympus EPOCH 650
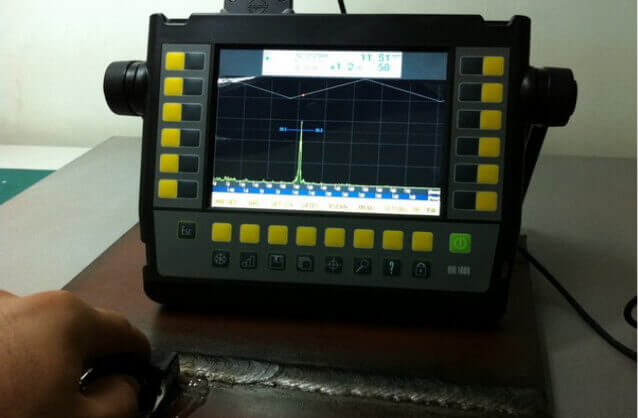
Ultrasonic defectoscop DIO 1000SFE made by czech producer STARMANS